Procurement management is a crucial aspect of construction that involves sourcing the right materials, services, and subcontractors to ensure a project is completed on time, within budget, and to the required standards. Understanding the different types of procurement and identifying who is responsible for managing these aspects can significantly influence a project’s success. Let’s dive into the essentials of procurement management in the construction industry.
It is all about the careful planning and coordination of resources to ensure that project timelines and budgets are met. It encompasses everything from selecting suppliers and negotiating contracts to purchasing goods and managing deliveries. The goal is to streamline all procurement activities to avoid delays and cost overruns, which are common pitfalls in the construction sector.
Effective procurement management strategy directly influences the quality of the construction, the efficiency of the project timeline, and the overall project cost. A well-managed procurement process not only ensures that materials arrive on time but also that they adhere to the necessary specifications and regulations.
Who is responsible for construction procurement management?
The responsibility for procurement management can lie with various parties, depending on the project’s management model:
The Owner: In smaller projects or in situations where the owner prefers direct control, the owner may take on the procurement responsibilities to oversee project costs and schedules closely.
Project Manager: Often, especially in larger projects, a dedicated project manager will handle procurement to ensure that the construction meets the project specifications and is aligned with the timeline and budget.
Procurement Manager/Specialist: Some firms have a dedicated procurement manager or specialist who focuses solely on procurement tasks, working alongside the project manager to optimize supply chain solutions.
General Contractor: Under certain contractual arrangements like design and build, the general contractor might oversee procurement, handling everything from material orders to hiring subcontractors.
Construction Manager: In a construction management setup, the construction manager may play a pivotal role in procurement, especially in selecting subcontractors and managing the construction phase.
Effective procurement management in construction is more than just choosing suppliers and subcontractors; it involves strategic planning, thorough knowledge of the market, and keen negotiation skills to secure the best materials and services at the most favorable costs.
Construction procurement management methods

1. Traditional Procurement (Design-Bid-Build): This is the most common method where the design phase is completed first, followed by bidding for construction contracts. It’s preferred for its straightforward, sequential approach.
2. Design and Build: Here, one entity works on both the design and construction, which can lead to faster completion times and potentially lower costs due to the integrated services.
3. Management Contracting: In this method, the management contractor is responsible for overseeing the entire construction operation, subcontracting different components of the work to various entities.
4. Construction Management: Similar to management contracting, but the construction manager acts more as a consultant to the owner and is involved more deeply in the procurement of subcontractors.
5. Public-Private Partnerships (PPP): This method involves collaboration between government entities and private companies, often used for large infrastructure projects requiring significant investment.
Each procurement management method offers different benefits and challenges, and the choice depends largely on the project scope, budget, timeline, and risk tolerance. Understanding these elements helps ensure that the procurement strategy aligns with project goals, paving the way for successful construction outcomes.
Steps involved in the construction procurement management process

1. Need Identification: It all starts with pinpointing what’s necessary for the project. This could range from raw materials like steel and concrete to specialized labor or technical services.
2. Budgeting: Once needs are identified, the next step is to estimate how much funding is required. This includes considering current market prices and potential future changes in costs.
3. Supplier Research and Selection: Finding the right suppliers is crucial. This step involves researching potential suppliers, evaluating their credibility, and ensuring they can meet the project’s quality and timeline requirements.
4. Tendering: This involves issuing a formal request for bids (tender) from potential suppliers. It’s a competitive process that helps ensure fair pricing and quality assurance.
5. Contract Negotiation and Awarding: After reviewing all tenders, the next step is to negotiate terms with the chosen suppliers. This includes finalizing payment terms, delivery schedules, and other contract specifics.
6. Order Management: Managing orders involves overseeing the delivery schedule, ensuring materials arrive on time, and coordinating with the project timeline to prevent any disruptions.
7. Inventory Control and Storage: Once materials are delivered, managing inventory effectively is essential to prevent loss or damage, ensuring materials are available when needed.
8. Closure and Review: After the project is completed, reviewing what went well and what didn’t can provide valuable insights for future procurement processes.
Types of procurement management in construction
- Materials: This involves the acquisition of all the building materials required for a construction project, such as cement, steel, wood, and bricks.
- Equipment: This type of procurement focuses on obtaining necessary construction machinery and tools, from cranes and bulldozers to hand tools and safety gear.
- Services: This includes securing professional services needed for construction projects, like architectural design, engineering, and project management.
Purchasing vs Procurement
In construction, “procurement” and “purchasing” might sound similar but they actually refer to different aspects of resource acquisition for a project. Procurement encompasses the full spectrum of activities, including planning, selecting, negotiating, and purchasing the essential goods, services, and tasks needed to finish a construction project. On the other hand, purchasing is specifically the action of buying these resources. It is merely a part of the larger procurement process, concentrating only on the transactional phase of acquiring materials, services, or equipment. Recognizing this difference is key to effectively managing the supply chain and achieving project success.
Challenges in construction procurement management
While the process can streamline project delivery, it also comes with its set of challenges:
- Market Fluctuations: Prices for materials can vary widely due to market conditions, which can affect budgeting and financial planning.
- Supply Chain Issues: Delays in the supply chain can stall projects, highlighting the need for effective logistics planning and management.
- Regulatory Compliance: Navigating the compliance requirements in different regions or countries can be complex and requires a thorough understanding of local regulations.
Role of the construction procurement manager
The role of a procurement manager is crucial for the success of any project. This role involves overseeing the process of acquiring all the necessary materials, services, and contracts required to complete a construction project. The benefits of effective procurement include improved timeliness, enhanced communication, better budget management, and minimized risks.
The benefits of effective procurement
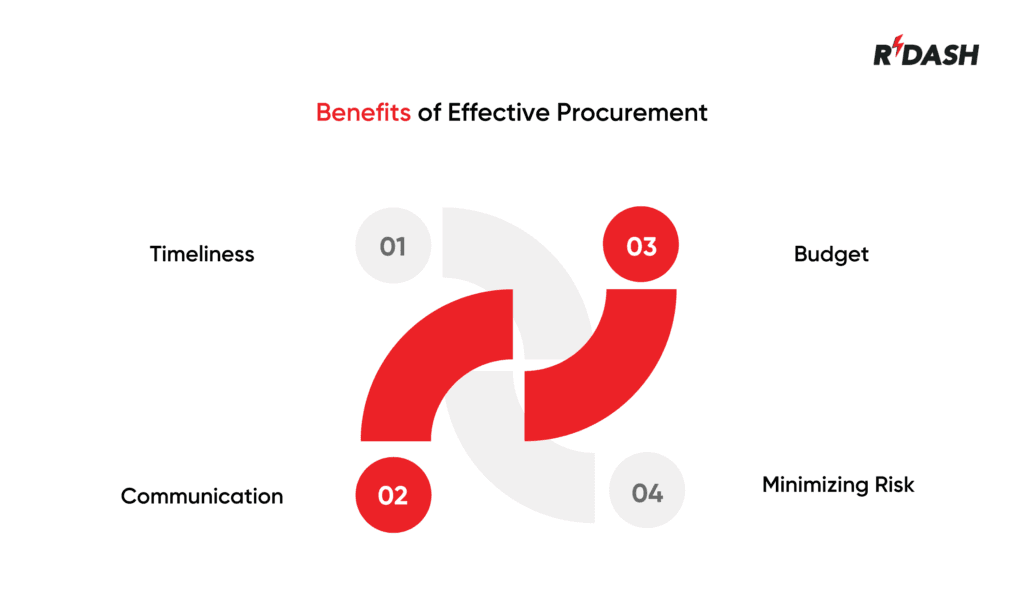
- Timeliness: Ensuring that materials and services are delivered on schedule is vital to keep a construction project on track. A skilled procurement manager can prevent delays by coordinating timely deliveries.
- Communication: Good procurement practices improve communication between suppliers, contractors, and the project management team, ensuring that everyone is clear on expectations and timelines.
- Budget: Effective procurement helps to manage and reduce costs by selecting the best suppliers who offer competitive pricing and good quality materials. This is crucial in keeping the project within its financial boundaries.
- Minimizing Risk: By carefully selecting reliable suppliers and ensuring contract compliance, a procurement manager can minimize the risks associated with overruns, subpar materials, or contract disputes.
FAQs
What are the types of procurement in construction?
In construction, the main types of procurement include traditional procurement, design and build, management contracting, and construction management. Each type has its own benefits and is chosen based on the project’s specific needs.
How do you develop a procurement strategy?
Developing a procurement strategy involves understanding the project requirements, identifying potential suppliers, evaluating their capabilities, and setting clear goals and criteria for selection. It also includes negotiating terms that benefit both the buyer and the supplier to ensure a smooth flow of resources.
What is the role of procurement in construction management?
Procurement management involves the strategic buying of goods and services needed to complete a construction project. This role is pivotal in managing costs, ensuring quality, and achieving timely completion of the project. Effective procurement strategies align with the overall project goals and ensure that resources are appropriately allocated.
How RDash can help
The construction procurement manager carries a heavy load of duties. This is where construction project management software becomes essential. RDash is a tool designed to assist construction procurement managers in planning, monitoring, and reporting their activities. It provides the necessary features to organize tasks, track progress live, and keep stakeholders informed, ensuring all parties are consistently aligned.