What is a punch list?
A punch list is a document used towards the end of a construction project to list any work remaining to be done or repaired before final payment. The list is usually created during a walk-through of the construction site between the project manager, contractor, and client. The intention of the punch list is to confirm that the work is at agreed standards and issues are repaired to the client’s satisfaction.
Why is it called a punch list?
The name “punch list” originated from the old practice of workers punching holes next to items on a list of things to repair. This served as a system to track each task being finished. Although the process no longer involves punching holes, the idea is the same. The list is a final list of tasks to “punch out” or finish the job.
How to Create a Punch List
Creating a good punch list involves a straightforward process:
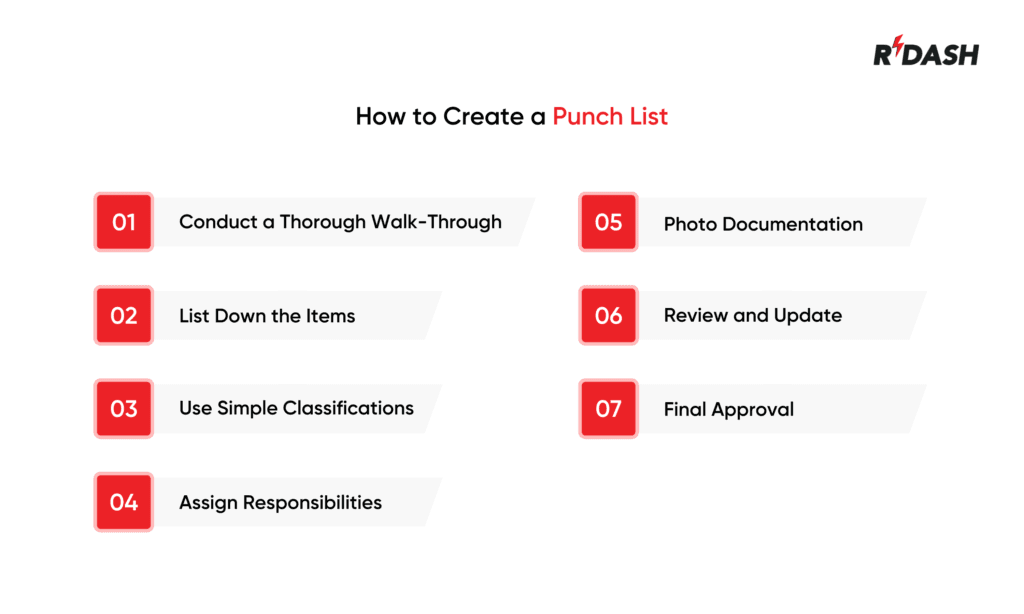
Conduct a Thorough Walk-Through: At the end of the job, take a detailed walk-through of the site. The walk-through is with the project manager, contractor, and client and ensures all interested parties are in agreement on what work needs to be done or repaired.
List Down the Items: During the walk-through, list down any outstanding tasks, defects, or areas of the site that are below the project’s standards. Examples include paint touching up, fitting installation, or any final cleanup that needs to be performed.
Use Simple Classifications: Put the items under classifications such as carpentry, plumbing, electric, etc. This makes it easy to assign tasks to relevant teams or staff.
Assign Tasks: Assign each task on the punch list to a specific contractor or team member clearly. Give a deadline for the completion of each item.
Assign Responsibilities: Clearly assign each task on the punch list to a specific contractor or team member. Include a deadline for when each item needs to be completed.
Photo Documentation: Take photos of the items to be repaired to make things clear and for record purposes. This ensures that everyone knows what specific issue needs to be repaired.
Review and Update: Update the punch list as the completion of the tasks continues and notify the client of the updates. Ensure that every task is completed to the satisfaction of the client before it is marked complete.
Final Approval: After the completion of all the items on the punch list, conduct a final walk-through with the client to ensure that all the work has been completed to the satisfaction of the client. The project is complete once the client signs off the final list.
Who is Responsible for the Punch List Items?
Responsibility to repair punch list items usually lies with the contractor or subcontractors who did the original work. The general contractor oversees the operations to repair the items, ensuring that all the work is completed to the specifications indicated in the construction contract. The client, along with the project manager or the architect, marks the issues or the outstanding work during a final walk-through of the project. Once indicated, the contractor is held responsible for doing the corrections required or for completing the outstanding work.
The responsibilities are usually given as follows:
General Contractor: Coordinates the whole process, ensures that the subcontractors have completed their work, and ensures that all the punch list items are repaired as per the contract provisions.
Subcontractors: Subcontractors who worked on items like electrical wiring, plumbing, or painting are responsible for repairing the issues that involve their work.
Architects or Engineers: May be brought in to verify the corrections are up to standards and design specifications, particularly structural or aesthetic repairs.
Client or Owner: Must review and sign off on completion of punch list items. Must clearly communicate to the contractor what they will accept and make sure they are satisfied before project completion.
Examples of Punch List Items
Punch list items may be fairly diverse depending on the type of construction project but often include such things as:
Items to Test
Testing verifies all the work installed, materials, and equipment function as desired. Typical tests included in punch lists are:
Appliances: To verify that they are in working order and efficient.
Equipment: To verify the equipment and tools used on the project function properly.
Doors & Windows: To verify smooth operation and proper closure.
Plumbing Fixtures: To verify for leaks, proper flow, and functionality.
Mechanical Elements: To verify that all mechanical components function as expected.
Communication Systems: To verify connectivity and function.
HVAC Systems: To verify that heating, ventilation, and air conditioning systems are in working order and efficient.
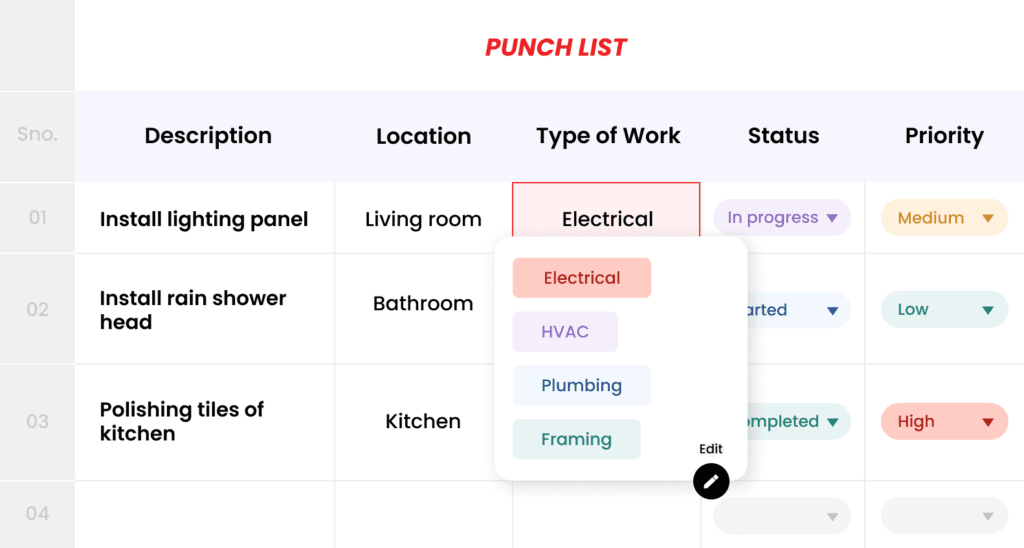
Items to Add
Additions would usually include things that were accidentally omitted from the original installation. They include:
Light Covers: Installing missing or temporary light covers.
Hardware: Installing knobs, handles, and fixtures omitted.
Paint Touch-Ups: Repairing missed areas or damage that occurred during construction.
Coating/Sealant: Adding protective coatings or sealants omitted.
Items to Fix
Repairs include correcting any damages or errors that occurred during construction. These repairs may include:
Leaks: Repairing any leaks in plumbing or on the roof.
Damaged Materials: Repairing or replacing items damaged during construction.
Improper Installation: Correcting any installations that are substandard.
Cracks: Repairing cracks in walls, floors, or foundations.
Defective Equipment: Repairing or replacing tools or machinery that are not functioning.
Items to Remove
Removals ensure the site is free of all temporary materials and equipment prior to handover:
Trash: Removing all construction waste and debris.
Equipment: Removing temporary construction equipment.
Extra Materials: Removing or recycling unused construction materials.
Tools: Making sure no construction tools are left on site.
Protective Covers: Removing temporary protective materials from the project.
This organized process of listing punch list items ensures that nothing is missed and the project is completed to the best standard.
How RDash can help
RDash increases the effectiveness of handling punch list items by providing a centralized platform on which tasks can be allocated to the responsible person. This enables project managers to monitor the real-time progress of each task. The transparency and accountability of RDash ensure all corrections are carried out promptly and to the standard required, reducing the completion of projects.