What is Overhead in the Construction Industry?
Overhead in the construction industry refers to the indirect costs required to run a construction business. These costs are not directly linked to a specific project but are essential for business operations. Overhead expenses include office rent, insurance, employee salaries, legal fees, and marketing costs.
Unlike direct costs such as materials and labor, overhead costs support the overall business rather than a single construction project. If not managed properly, these expenses can reduce profits and make pricing projects accurately more difficult.
Why do you need to calculate overhead costs?
Determining overhead costs is crucial for multiple reasons:
1. Accurate Project Bidding
When preparing a bid, a contractor must factor in overhead costs to ensure that the final price covers both direct expenses and business operations. Underestimating these costs can result in financial losses.
2. Profitability Management
Understanding overhead costs helps construction companies track where their money is going and find ways to improve efficiency. If overhead expenses are too high, profits will shrink even if projects are completed on time and within budget.
3. Better Financial Planning
A clear understanding of overhead allows businesses to make informed decisions about hiring, purchasing equipment, and expanding operations. It also helps in setting realistic goals for revenue and profit margins.
4. Competitive Pricing
By properly allocating overhead costs, construction companies can set competitive prices while maintaining profitability. This ensures they can compete effectively without taking on unprofitable projects.
Types of construction costs and expenses
Construction costs can be broadly divided into three categories: direct costs, indirect costs, and overhead costs.
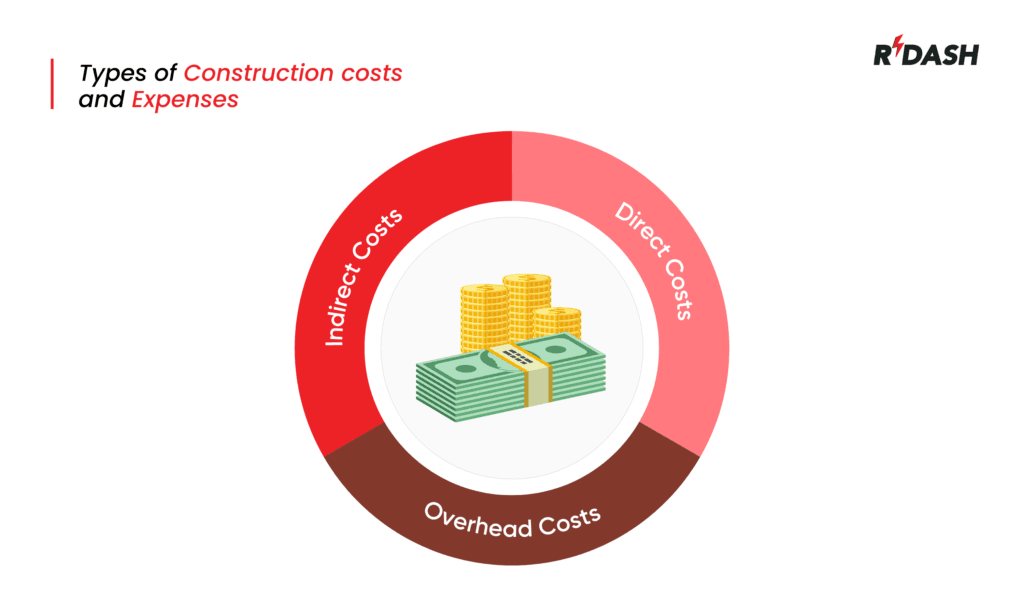
1. Direct Costs
These are costs directly related to a construction project. They include:
- Materials – Concrete, steel, lumber, electrical wiring, and plumbing supplies.
- Labor – Wages paid to workers such as masons, carpenters, and electricians.
- Equipment – Rental or purchase of machinery like cranes, bulldozers, and scaffolding.
2. Indirect Costs
Indirect costs are expenses related to multiple projects but not directly tied to a specific one. These include:
- Project Management Salaries – Payments to site supervisors, safety officers, and other administrative personnel.
- Permits and Licenses – Government fees for construction approvals.
- Temporary Facilities – On-site office spaces, security, and fencing.
3. Overhead Costs
Overhead costs are the expenses that keep a construction business running, regardless of ongoing projects. They can be divided into:
Fixed Overhead Costs
These costs remain constant regardless of business activity. Examples include:
- Office Rent – Monthly lease payments for corporate offices.
- Salaries – Payments to administrative staff such as accountants, HR personnel, and executives.
- Insurance – Coverage for liability, workers’ compensation, and property damage.
Variable Overhead Costs
These costs fluctuate based on the volume of work. Examples include:
- Marketing and Advertising – Website maintenance, promotional campaigns, and client meetings.
- Office Supplies and Utilities – Electricity, internet, and office equipment.
- Travel Expenses – Site visits, business meetings, and transportation.
How to make your estimates more accurate
Accurately estimating overhead costs is essential for construction companies to maintain profitability and remain competitive. If overhead costs are underestimated, a company may end up with lower profit margins or even financial losses. On the other hand, overestimating overhead can lead to inflated project bids, making it difficult to win contracts.
Here are some effective strategies to improve the accuracy of overhead estimates:
1. Track Historical Data
Review past projects and financial records to understand overhead trends. Analyzing previous costs will provide insights into spending patterns and help in making realistic estimates for future projects.
2. Categorize Costs Clearly
Divide overhead expenses into fixed and variable costs. Fixed costs, such as rent and insurance, remain constant, while variable costs, like marketing and fuel expenses, fluctuate based on business activity. Proper categorization helps in creating more precise estimates.
3. Use Cost Allocation Methods
Allocate overhead costs to individual projects based on realistic factors such as labor hours, equipment usage, or project size. This ensures each project carries its fair share of business expenses.
4. Adjust Estimates for Inflation
Over time, costs such as materials, salaries, and insurance tend to rise. Factor in inflation and market trends while estimating overhead costs to prevent budget shortfalls.
5. Monitor and Update Regularly
Overhead costs change as a business grows or market conditions shift. Regularly update estimates based on new data, project requirements, and economic changes. A monthly or quarterly review can help keep estimates accurate.
6. Use Construction Accounting Software
Allocate funds toward software that monitors and evaluates expenses instantaneously. Modern accounting tools help automate calculations, reduce errors, and provide better financial insights.
7. Consider Seasonal Variations
Construction companies often experience seasonal changes in workload. During slow months, overhead costs may remain the same even if revenue decreases. Adjust estimates accordingly to ensure financial stability.
By following these strategies, construction businesses can develop more accurate overhead estimates, leading to better pricing, improved financial planning, and increased profitability.
What is included in overhead costs in construction?
Overhead costs in construction refer to the indirect expenses required to operate a business. These costs are not directly tied to a single project but are necessary for overall business operations. Overhead costs can be categorized into two main types: fixed overhead costs and variable overhead costs.
1. Fixed Overhead Costs
These expenses remain constant, regardless of the number of projects a company handles. They include:
- Office Rent or Lease – Costs associated with maintaining a corporate or regional office.
- Salaries of Administrative Staff – Payments to employees who are not directly involved in project execution, such as HR, accountants, and management.
- Insurance – Includes general liability insurance, workers’ compensation, vehicle insurance, and property coverage.
- Depreciation of Equipment – The reduction in value of company-owned machinery, computers, and tools over time.
- Legal and Accounting Fees – Professional services required for business operations, tax filing, and compliance.
2. Variable Overhead Costs
These costs fluctuate based on the number of active projects and business operations. Examples include:
- Utilities and Office Supplies – Expenses for electricity, internet, water, and office materials.
- Marketing and Advertising – Costs for business promotion, website maintenance, and client acquisition.
- Travel and Accommodation – Site visits, client meetings, and employee travel expenses.
- Training and Development – Expenses for employee skill enhancement and certifications.
- Temporary Staff or Contract Workers – Payments for additional workforce needed for short-term projects.
3. Job-Site Overhead Costs
While not considered direct costs, some expenses specific to job sites are included in overhead:
- Equipment Rental – Costs for renting machinery that is used across multiple projects.
- Site Security and Safety Compliance – Costs for security personnel, safety gear, and regulatory compliance.
- Permits and Legal Approvals – Fees required for obtaining project licenses and government clearances.
Step-by-Step guide to calculating overhead costs
Calculating overhead costs accurately is crucial for construction companies to ensure they cover all indirect expenses and remain profitable. Using an overhead rate is a common method to allocate these costs effectively across various projects. Here’s a straightforward guide on how to calculate your overhead costs using the overhead rate, without diving into specific examples or formulas:

Step 1: Identify All Overhead Costs
Start by listing all the overhead expenses that your construction company incurs. These typically include administrative salaries, office rent, insurance, utilities, marketing, and more. Ensure you capture every recurring cost that is not directly tied to a specific project.
Step 2: Choose a Basis for Allocation
Select a basis for allocating overhead costs to projects. This could be total labor hours, labor costs, or materials cost — whichever reflects the usage of resources most accurately for your business.
Step 3: Calculate Total Overhead Costs
Add up all the overhead costs identified in step 1 for a specific time period, such as monthly or annually. This total will be used in conjunction with the allocation basis from step 2.
Step 4: Determine Total Allocation Base
Sum up the total amount of the base you chose in step 2 across all projects. For instance, if you chose labor hours, calculate the total hours worked on all projects during the period you are considering.
Step 5: Calculate the Overhead Rate
Apportion the aggregate overhead expenses across the comprehensive base of allocation. This gives you the overhead rate, which represents the amount of overhead cost associated with each unit of the allocation base.
Step 6: Apply the Overhead Rate
To find out the overhead cost for a specific project, multiply the overhead rate by the amount of the allocation base used by that project. This will give you the portion of overhead costs attributed to the project based on its resource usage.
Step 7: Regularly Update Calculations
Review and update your overhead calculations regularly. Overhead costs can change due to new hires, changes in insurance rates, office expansions, or other factors. Regular updates ensure that your pricing remains accurate and reflective of current business costs.
Step 8: Monitor and Adjust
Finally, monitor the impact of overhead costs on your overall financial health. If overhead seems too high relative to your revenue, consider ways to reduce costs or improve efficiency. Adjustments may be needed to ensure that the business remains competitive and profitable.
Mistakes to avoid in construction overhead
Mismanaging overhead costs can lead to financial losses and reduced competitiveness. Here are some common mistakes construction companies should avoid:
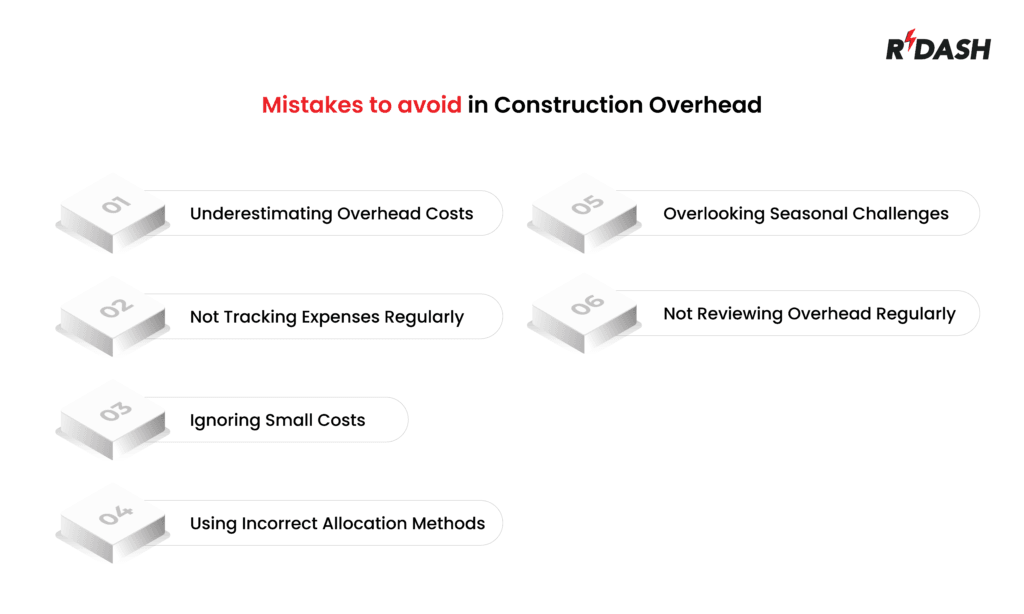
1. Underestimating Overhead Costs
Many contractors only focus on direct costs and ignore overhead expenses, leading to pricing errors and lower profits. Always factor in fixed, variable, and job-site overhead costs when estimating projects.
2. Not Tracking Expenses Regularly
Failing to track overhead costs consistently can result in budget overruns. Use accounting software or spreadsheets to monitor expenses and adjust estimates when needed.
3. Ignoring Small Costs
Minor expenses like fuel, office supplies, and internet bills can add up over time. Ensure that every cost, no matter how small, is recorded and included in overhead calculations.
4. Using Incorrect Allocation Methods
Some businesses allocate overhead costs equally across all projects, which can be misleading. Instead, use a cost allocation method based on direct labor hours, project size, or revenue contribution to distribute overhead fairly.
5. Overlooking Seasonal Changes
Construction workloads fluctuate due to weather conditions, market demand, and project cycles. Adjust overhead estimates to account for slow seasons when business expenses remain the same but revenue drops.
6. Not Reviewing Overhead Regularly
Costs change due to inflation, new hires, or expanded operations. Regularly review overhead expenses and adjust the overhead rate to reflect updated financial conditions.
By avoiding these mistakes, construction businesses can improve cost control and ensure sustainable growth.
How to reduce your overhead costs
Reducing overhead costs without compromising productivity is crucial for construction businesses. Here are effective ways to cut unnecessary expenses and improve profitability:
1. Automate Administrative Tasks
Using construction management software can streamline payroll, invoicing, and expense tracking, reducing the need for excessive administrative staff.
2. Outsource Non-Core Functions
Instead of hiring full-time employees for specialized tasks like legal work, IT support, or marketing, consider outsourcing these services on a contract basis to reduce payroll costs.
3. Optimize Office Space
If possible, downsize office space or switch to a hybrid work model to save on rent, utilities, and office supplies.
4. Negotiate Better Supplier Deals
Renegotiate contracts with suppliers, subcontractors, and service providers to get bulk discounts or better payment terms.
5. Reduce Travel and Accommodation Costs
Encourage virtual meetings and limit unnecessary travel to reduce expenses related to transportation and lodging.
6. Improve Energy Efficiency
Switching to energy-efficient lighting, optimizing HVAC usage, and implementing energy-saving practices can reduce utility bills.
7. Lease Instead of Buying Equipment
For machinery that is not used daily, leasing instead of purchasing can help lower maintenance and storage costs.
8. Cross-Train Employees
Encourage cross-training so employees can handle multiple responsibilities, reducing the need for hiring additional staff.
9. Monitor and Eliminate Waste
Regularly review overhead expenses and eliminate unnecessary costs such as unused software licenses, excessive inventory, or redundant processes.
10. Plan for Seasonal Variations
During slower months, reduce overhead expenses by scaling down operations, negotiating temporary cost reductions, or delaying non-essential expenditures.
Common mistakes when calculating overhead costs
Calculating overhead costs in the construction industry involves attention to detail and strategic planning. Mistakes in this process can lead to underestimations that affect a company’s profitability or overestimations that make bid proposals less competitive. Here’s a look at some common errors businesses make during this crucial calculation:
1. Not Including All Overhead Costs
One of the most frequent mistakes is failing to account for all overhead costs. Items like small tools, office supplies, and even employee training sessions can be overlooked but can add up significantly over time.
2. Overlooking Seasonal Variations
Construction companies often experience fluctuations in work volume due to seasonal changes. Failing to adjust overhead allocations during different seasons can result in inaccuracies that affect the financial health during off-peak periods.
3. Using Outdated Information
Relying on historical data without considering recent changes in the business environment can lead to inaccurate overhead rates. Changes in rental costs, insurance premiums, or administrative salaries should be reflected in the overhead calculations.
4. Inconsistent Allocation Methods
Inconsistency in the basis used for allocating overhead costs (like switching between labor hours and material costs without justification) can cause inconsistencies in pricing and profitability analyses across projects.
5. Ignoring Indirect Labor Costs
Sometimes, the salaries of indirect employees who support multiple projects (like project managers or safety officers) are not fully considered. This can undervalue the overhead needed to support ongoing operations.
6. Lack of Regular Updates
Failing to regularly update and review overhead costs leads to discrepancies between actual expenses and what is charged in project bids. Regular reviews help adjust for changes and ensure accuracy.
By being aware of these common mistakes and actively working to avoid them, construction companies can significantly improve the accuracy of their overhead cost calculations.
Control Your Overhead Costs in Real-Time With RDash
In today’s competitive construction industry, managing overhead costs effectively is crucial for maintaining profitability and operational efficiency. RDash offers a dynamic solution that allows businesses to control and monitor their overhead costs in real-time.
Real-Time Monitoring
RDash provides a dashboard that updates overhead costs as they are incurred, giving managers immediate insights into how much is being spent on non-direct project expenses like administrative salaries, office utilities, and more.
Customizable Alerts
Set up alerts in RDash to notify you when overhead costs are nearing preset thresholds. This proactive feature helps prevent budget overruns and ensures that overhead costs do not exceed planned amounts without your knowledge.
Detailed Reporting
With RDash, you can generate detailed reports that break down overhead costs by category, project, or period. This granular insight helps identify trends and areas where savings can be achieved.