A Bill of Materials (BOM) serves as a comprehensive guide for construction and manufacturing processes, detailing everything from basic materials to production steps. It encompasses not only materials but also assembly components, product structures, and instructions for procurement. Crucially, a BOM facilitates the management of complex supply chain processes, including inventory planning, task scheduling, and cost estimation.
By providing insight into required materials and quantities, BOMs aid in procurement, cost estimation, inventory control, and waste reduction, thus minimizing project delays and failures. They come in various types such as Single-level and Multi-level BOMs, each organized hierarchically to represent the structure or product and its constituent components. Despite its apparent simplicity, creating and managing BOMs can be challenging, particularly for projects with numerous parts.
BOMs are essential tools in construction and manufacturing, offering detailed inventories and instructions for producing specific structures or products. They streamline supply chain processes by aiding in material procurement, cost estimation, and inventory management.Despite their importance, managing BOMs can be complex, especially for projects with numerous components, requiring meticulous attention to detail and organization.
B.O.M Vs B.O.Q
Aspect | B.O.M. (Bill of Materials) | B.O.Q. (Bill of Quantities) |
---|---|---|
Purpose | Defines materials, components, and parts needed for a project | Lists quantities of materials, labor, and services for specific tasks |
Content | Material list with descriptions and quantities | Quantity breakdowns for materials, labor, and services |
Focus | Materials and components needed for construction or manufacturing | Quantities and costs associated with tasks or activities |
Usage | Procurement, assembly, and construction planning | Cost estimation, tendering, and contract management |
Industry | Manufacturing, construction | Construction |
Key Function | Ensure accurate procurement and assembly | Facilitate cost estimation and bidding processes |
What makes the Bill of Materials (BOM) indispensable?
A Bill of Materials (BOM) is essential for efficient and accurate project execution in both product manufacturing and construction endeavors. By providing a comprehensive list of required components and materials, a BOM enables companies to assess their readiness for a project and anticipate any potential delays or shortages beforehand. Through early estimation of component costs, facilitated by the BOM, companies can ensure they have adequate resources to complete the project within budget and on schedule. This proactive approach minimizes the risk of material shortages and allows contractors to deliver the final product confidently. Ultimately, a well-prepared BOM empowers companies to execute projects smoothly, meet client expectations, and maintain project timelines and budgets effectively.
Bill of Materials Components
Bill of Materials Components
Typically, BOMs comprise the following elements crucial to a project:
BOM Level: This signifies the hierarchical position of a specific component within the BOM structure. For instance, in the context of a commercial building BOM, the top level may encompass all raw materials like cement, aggregate, reinforcement, precast components, etc., needed for constructing certain sections of the building. These materials are then integrated into the next level, which represents the assemblies required to form the final structure. Assigning BOM levels helps organize materials systematically.
Part Number: A unique identifier used to swiftly recognize individual materials or components by anyone involved in the project or production process. The description accompanying a part number is often crucial in pinpointing the exact material. Part numbers can be categorized into intelligent and non-intelligent types. Intelligent part numbers may contain alphanumeric codes or detailed descriptions, while non-intelligent ones typically consist of numeric codes. These identifiers streamline material identification, provided the person assigning them is well-versed in the details of each component.
Part Name: Similar to part numbers, part names serve as identifiers for components, though they may not always be unique. Companies employ part names for organized tracking of components, often using internal references to tasks or operations. Consistency in part naming ensures clarity among employees when identifying materials or parts.
Phase: BOMs play a crucial role in categorizing components based on the stages in which they are needed. This designation indicates whether an element has been approved for procurement, released for use, or assigned to specific tasks.
Descriptions: component descriptions provide essential details such as characteristics, versions, etc., pertinent to the production process. These descriptions are unique to individual parts and offer more comprehensive information than part numbers or names.
Measurement Unit: Indicates the scale on which each material type is to be procured or utilized, ensuring precise ordering of required quantities. Measurement units vary, ranging from pieces to kilograms or pairs to liters.
Procurement Type: Specifies the method for obtaining all necessary components for the construction project, including purchasing, local production, or subcontracting to third-party manufacturers.
Reference Pointers: Advanced technologies are are used to pinpoint the location and dynamic characteristics of components. For instance, circuit boards can be employed to aid in component identification.
BOM Notes: Additional information accompanying the BOM serves as useful supplements for anyone referencing the document. These notes may include details about materials or alternative supplier information.
Bill of Materials Structures
Bill of Materials Structures BOMs can be organized in two distinct formats to convey essential project information:
Single-level BOM: This type presents all necessary production elements and their respective quantities, resembling a straightforward shopping list. While easy to create and analyze, single-level BOMs lack the depiction of relationships between parts, such as assemblies, sub-assemblies, and components. Consequently, identifying the cause of failure in a specific section of a structure for repair or replacement becomes challenging. Complex products within single-level or ‘flat’ BOMs may thus pose difficulties in comprehension and supply chain management.
Multi-level BOM: In contrast, multi-level BOMs illustrate the interconnections among various project components, including assemblies and sub-assemblies. These BOMs establish relationships by indenting supplies or sub-assemblies that compose the subsequent levels of parts or assemblies, often referred to as Indented BOMs. Grouping related items into logical subgroups aids in identifying part sources from specific suppliers or distribution channels.
Based on the specific information to be incorporated, BOMs are categorized into three primary types:
Engineering BOM: Developed during product design, this BOM outlines the original design of the finished product.
Sales BOM: Used to list components and assemblies required to fulfill a client’s specifications, generated from sales orders and encompassing both final products and manufacturing components.
Manufacturing BOM: Employed in production processes, MBOM delineates parts and assemblies necessary for product manufacturing, including packaging and accounting for production waste. This BOM aids in reviewing distinct sets of parts at each stage, along with processing requirements before assembly, facilitating timely material procurement and manufacturing operations to meet delivery schedules.
Other commonly used BOMs based on the the included information include Configurable BOM, Production BOM, Assembly BOM, and Template BOM.
How to Generate BOM?
Generating a BOM for faster payment processing:
- Define Data Inclusion: Compile a detailed list of all necessary materials, ensuring even minor components are accounted for to guarantee timely availability.
- Centralize BOM Data: Consolidate project-related information into a centralized repository, irrespective of departmental sources, for a unified record.
- Limit BOM Editors: Reduce the risk of errors by assigning editing responsibilities to a small, proficient team.
- Track BOM Revisions: Implement tracking mechanisms to document frequent revisions accurately, reflecting project dynamics.
- Choose BOM Structure: Decide on a single-level or multi-level BOM structure based on project needs.
- Initiate Itemization: Begin listing materials, components, and parts required for tasks, anticipating expansion over time.
- Maintain List Regularly: Continuously update the BOM with additional materials as needed, meticulously recording changes for accuracy.
Selecting the Right B.O.M. Software
Efficient BOM preparation and monitoring enhance construction project management, facilitated by modern project management tools tailored for the industry.
When searching for a BOM management solution, it’s vital to find a tool tailored to the needs of small to mid-sized manufacturers, supporting both short-term and long-term product development strategies.
Three essential features to prioritize in a BOM management tool are:
- Empowerment of Data Framework: The tool should establish the BOM as the central data framework, acting as the primary source of product data accessible throughout the organization.
- Integration of Collaborative Workspace: It should offer a collaborative workspace where design team members can engage with BOM data, encouraging progress, visibility, and smoother operation across the design chain.
- External Accessibility: The tool should enable access beyond organizational boundaries, facilitating integration between the design and supply chains for seamless collaboration in product development.
A BOM management tool that incorporates these aspects enhances the efficiency of individual users’ BOMs and promotes extensive data sharing across all levels of the supply chain.
Navigating Five Major B.O.M. Pitfalls
Ensuring Quantity Accuracy:Quantity discrepancies often arise from missing parts or inaccuracies in cost rollup calculations during product cost assessment, inventory management, or erroneous stock information. These factors can impede the the timely acquisition of the correct parts at the designated cost.
Addressing Missing Components in the BOM: Omissions in the BOM frequently stem from incorrect data export from design software or oversight in including specific items, often due to manual entry and lack of collaborative input.
Avoiding Costing Errors: Neglecting to verify costs and components during initial design phases can have costly consequences, affecting both final unit pricing and the product’s market success or failure.
Meeting Requirements:Failure to fulfill requirements, such as accurate component quantities, inventory precision, or inclusion of all necessary parts, as well as accurate cost estimations, can lead to significant delays and setbacks in production, impacting profitability and timelines.
Providing Adequate Documentation: Insufficient documentation, such as missing assembly instructions, material specifications, or safety guidelines, can result in production delays, material waste, compromised product quality, increased safety risks, and revenue loss.
Reducing BOM Errors with Better Practices: Implementing a product lifecycle management (PLM) solution can effectively address common BOM mistakes associated with manual data entry and fragmented spreadsheets. PLM offers a centralized platform for BOM management, providing real-time visibility and collaboration among internal teams and manufacturing partners, thereby reducing reliance on error-prone processes and enhancing efficiency.

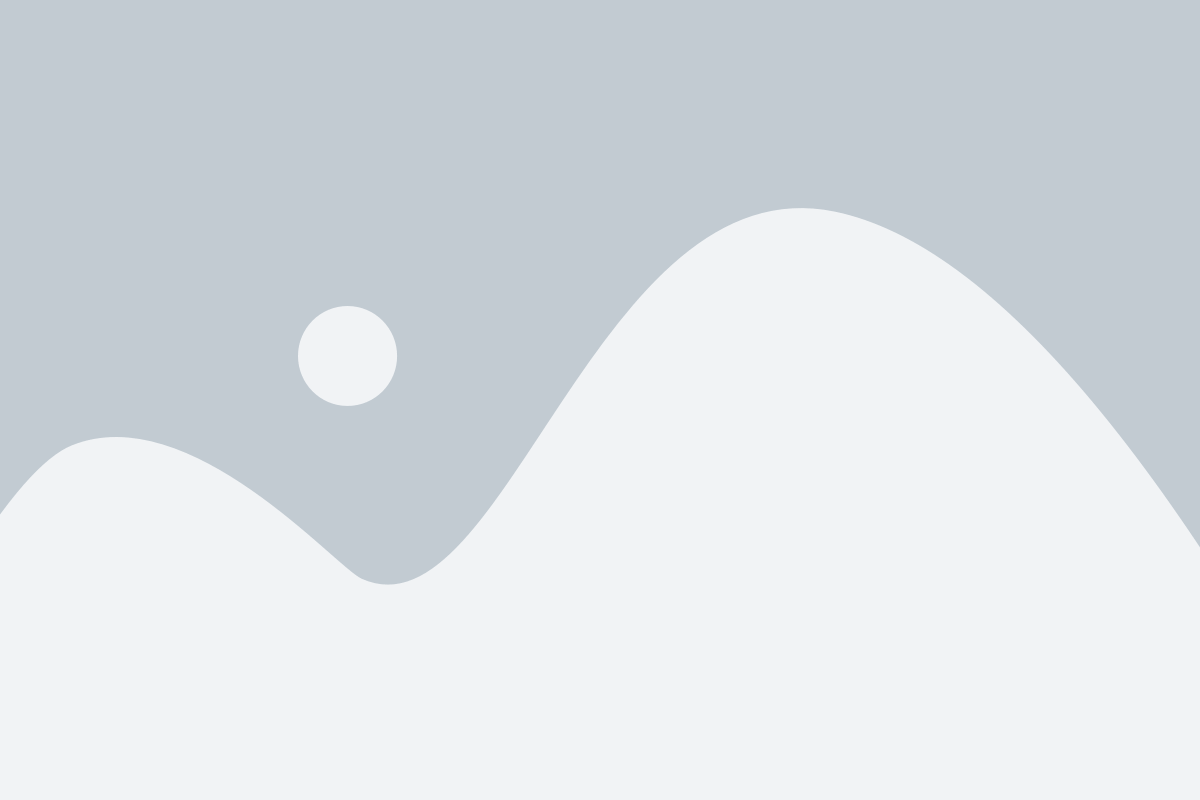