What is QA in construction?
Quality Assurance (QA) in construction is all about making sure that the right systems, processes, and standards are in place before any actual work starts. QA is a proactive approach that sets up guidelines, checks, and procedures so that everyone knows how to maintain quality throughout the project.
For example, QA involves setting clear specifications, using approved materials, and training teams on standard practices. It covers the planning and design stage, the selection of suppliers and subcontractors, and even the communication flow between teams.
When a company has strong QA processes, it means they’re less likely to run into unexpected issues later. The goal is to “do it right the first time” by preventing mistakes, rework, and cost overruns.
Good QA also means clear documentation. From project plans to method statements and checklists, everything should be well-recorded. This makes it easier to track progress, ensure compliance with local standards, and keep clients confident in the quality of work.
What is QC in construction?
Quality Control (QC) in construction is not exactly the same as QA. While QA is about setting up the system, QC is about inspecting the actual work on site to make sure it meets the standards. QC is more reactive, focusing on finding and fixing any defects during or after construction.
For example, QC activities include site inspections, testing materials, checking workmanship, and ensuring that installations match the approved plans. Inspectors or site engineers carry out regular checks to catch mistakes early. If they find any problems, the team must fix them before moving to the next stage.
QC is important because it protects the project from poor workmanship, unsafe practices, or substandard materials. By checking every step, QC helps avoid bigger issues later, like structural failures, leaks, or costly repairs after handover.
Proper QC also builds trust with clients. When they see that checks and tests are happening regularly, they feel more confident about the project’s safety and quality.
Difference Between Construction QA vs QC
Many people mix up QA and QC, but in construction, they play different roles.
Quality Assurance (QA) is process-focused. It’s about planning, creating systems, and setting standards before the work begins. Think of QA as the roadmap that guides everyone on how to do their job the right way, from design to completion.
Quality Control (QC) is product-focused. QC is about monitoring and testing the work while it is happening to find errors, defects, or anything that does not match the plan. If something is wrong, QC makes sure it’s fixed before moving on.
In short:
- QA = Preventing mistakes through systems and standards
- QC = Finding and correcting mistakes through checks and tests
When done together, QA and QC help construction companies deliver projects that meet high standards and keep clients happy.
How to Improve QA in Construction
Improving QA doesn’t have to be complicated – it just needs clear processes and team commitment. Here are some practical steps to improve QA:
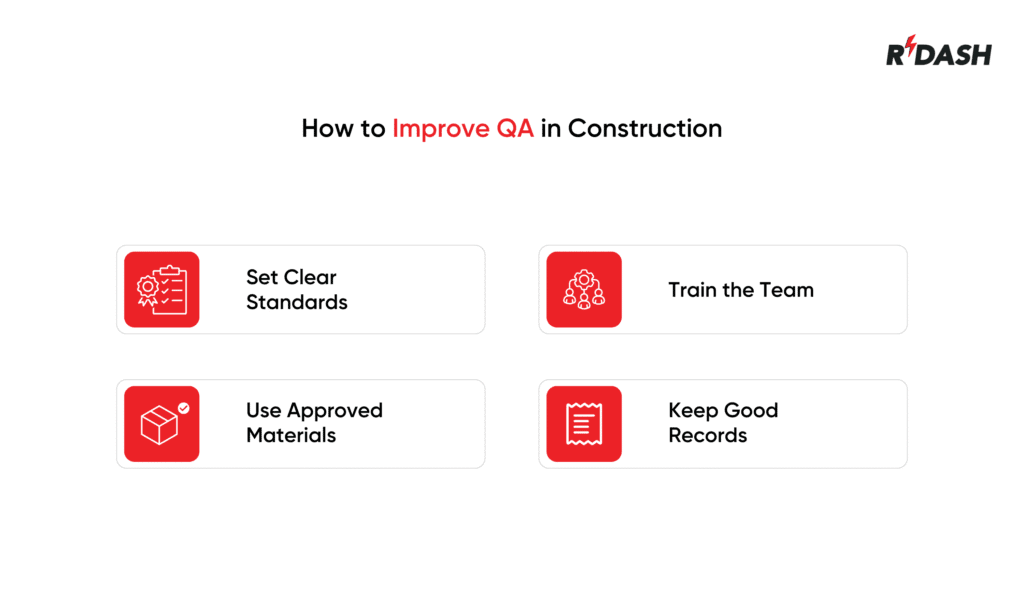
Set Clear Standards: Develop easy-to-follow guidelines for every part of the project – from design to handover.
Use Approved Materials: Always check that materials meet industry standards before using them on site.
Train the Team: Make sure everyone — from managers to laborers — understands the quality standards and what’s expected of them.
Keep Good Records: Maintain up-to-date drawings, specifications, and method statements. Keeping clear records helps teams check compliance more easily later.
Work With Trusted Vendors: Choose suppliers and subcontractors with a proven record of delivering good-quality work.
How to Improve QC in Construction
For QC, the focus is on better site inspections and clear reporting. Here’s how to do that:
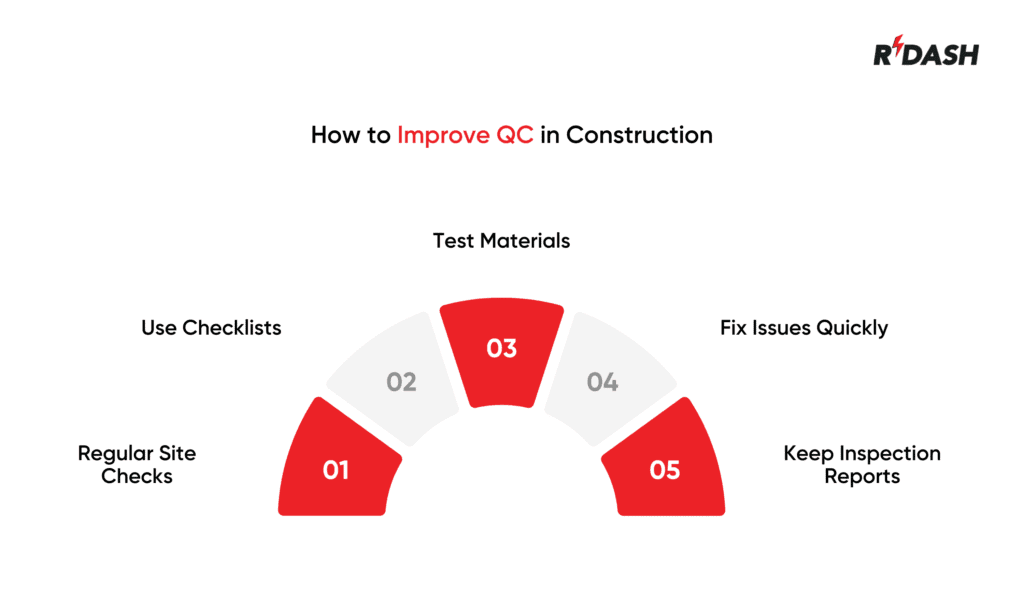
Regular Site Checks: Inspect work daily or weekly, depending on the stage of the project. This helps catch mistakes early.
Use Checklists: A simple checklist can make sure nothing is overlooked during inspections.
Test Materials: Always test materials like concrete or steel to confirm they meet project requirements.
Fix Issues Quickly: If an inspection finds a defect, fix it right away. Delays can make small issues turn into big problems.
Keep Inspection Reports: Document every inspection. Good records help settle disputes and keep clients confident in your work.
FAQs
1. What is the main difference between QA and QC in construction?
Quality Assurance (QA) focuses on setting up good systems and clear standards to stop mistakes before work begins. Quality Control (QC) checks the work and materials during construction to find and fix any problems.
2. Why are both QA and QC needed on construction sites?
QA helps teams plan better and follow best practices, while QC ensures the final work meets those plans and standards. Having both QA and QC in place helps reduce rework, saves money, and delivers better results.
3. Who is responsible for QA and QC?
Everyone plays a part. Project managers and quality engineers usually handle QA by setting up procedures. Site engineers, supervisors, and inspectors focus on QC by doing regular checks and tests.
4. How do you measure QA and QC performance?
QA can be measured by how well teams follow processes, training records, and audit results. QC is measured through inspection reports, defect rates, test results, and whether work passes client approvals.
5. How can using technology make QA and QC stronger?
Digital tools and construction management software like RDash make it easier to set standards, track inspections, store documents, and share updates in real time. This improves both QA planning and QC monitoring.
6. What happens if you ignore QA and QC?
Skipping QA or QC often leads to poor workmanship, delays, budget overruns, safety issues, and unhappy clients. In the worst cases, you may face rework, disputes, or legal trouble.