Construction labor cost is a critical component in any building project, affecting the overall budget and financial planning. It encompasses various expenses related to the workforce needed to complete a construction job. Here’s a breakdown of what construction labor costs include:
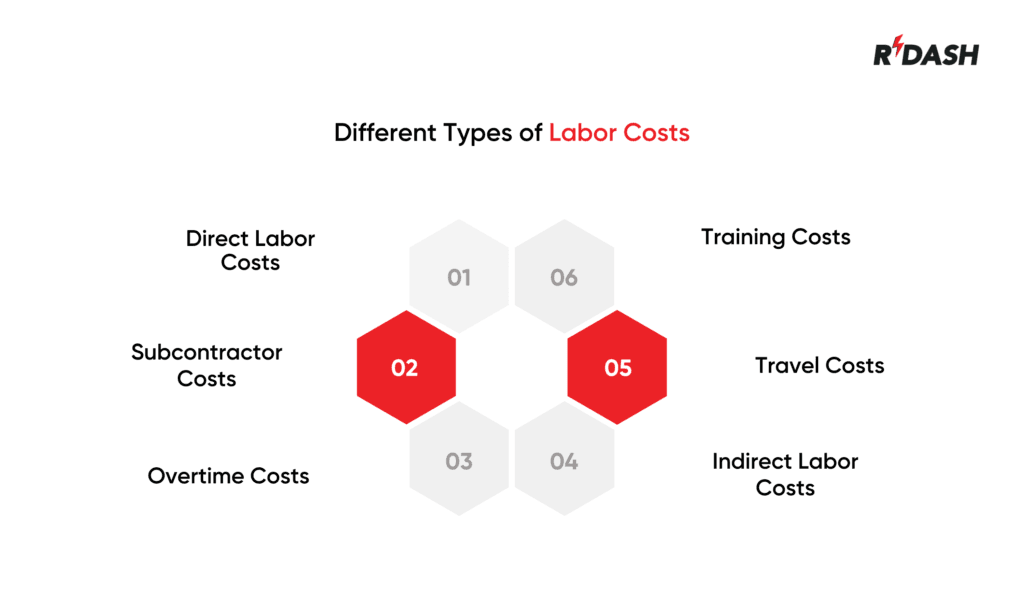
- Direct Labor Costs: These are payments made directly to construction workers who are on the payroll. Direct labor costs include wages, salaries, and any bonuses or benefits provided to the workers who physically construct the project.
- Subcontractor Costs: Often, construction projects require specialized skills that the main contracting company may not possess. Subcontractors are hired for specific tasks like electrical work, plumbing, or roofing. Costs incurred in hiring subcontractors are a significant part of the labor costs.
- Overtime Costs: Construction projects often have strict deadlines. When projects need to accelerate or catch up to a schedule, workers may need to put in extra hours. Overtime costs, which are higher than regular wages, compensate for the extended work hours.
- Indirect Labor Costs: These costs are not directly tied to the physical construction but are necessary for supporting the project. Indirect labor includes the salaries of supervisors, safety officers, and other non-construction personnel who play a crucial role in project completion.
- Travel Costs: In cases where construction sites are distant from workers’ regular places of work or where materials need to be transported from far off, travel costs will factor into the labor expenses. This can include the cost of fuel, vehicle maintenance, and lodging for workers.
- Training Costs: The construction industry frequently updates its methods and materials. Training costs ensure that workers are up-to-date on the latest construction techniques and safety regulations, which is vital for maintaining quality and safety standards.
How to Calculate Labor Cost in Construction
Calculating construction labor costs is crucial for budget planning and management. Here’s a basic guide on how to calculate these costs:
Determine Hours Worked: Estimate the number of hours each worker will spend on the project. Include both direct labor hours and any expected overtime.
Calculate Hourly Rates: Include wages, taxes, insurance, and benefits to get the total hourly cost of each worker.
Include Subcontractor Fees: If subcontractors are used, add their fees to the labor costs. Ensure to account for any markups or additional expenses they charge.
Factor in Indirect Costs: Add costs for labor-related expenses that are not directly linked to physical construction, such as project management, supervision, and transportation.
Sum Up Total Labor Cost: Add all the above costs to get the total labor cost for the project. This will help in assessing the financial feasibility and setting up the project budget.
Understanding these aspects helps in making informed decisions about resource allocation and financial planning, ensuring that the project remains on track and within budget.
Hiring Subcontractors or Self-Performing
Contractors have two primary options for managing their workforce: self-performing the work or hiring subcontractors. Self-performing contractors handle most of the project’s tasks themselves and generally incur higher labor costs. In contrast, general contractors often delegate specialized tasks to subcontractors, which can help control labor expenses.
The cost of labor can significantly vary between projects. Contractors who usually self-perform need to accurately predict labor costs to maintain profitability. They achieve this by referring to historical data from past projects, estimating the time required for various tasks, and then applying current wage rates to forecast the total labor cost for a new project.
Although labor costs have risen over time, their percentage of total construction costs has remained relatively constant. This stability occurs because increases in wages are often matched by rises in overhead and material costs.
Why it is important to keep construction labor costs under control
Managing labor costs in construction is crucial due to its direct impact on the overall project budget. Keeping these costs under control helps ensure the financial stability of a project, preventing budget overruns that can jeopardize profit margins and overall project success. Effective labor cost management also enhances the ability to bid competitively on future projects while ensuring sufficient resources are available to maintain high standards of quality and safety.
Stay on Budget: Managing labor costs effectively helps ensure that projects stay within the allocated financial resources, preventing budget overruns.
Allocate Resources Effectively: Controlled labor costs allow for better allocation of resources across various aspects of the project, ensuring that no single area unnecessarily consumes the budget.
Be More Productive: Efficient use of labor leads to higher productivity. When labor costs are managed well, teams can focus on achieving more in less time, with fewer resources wasted.
Finish Projects on Time: Keeping labor costs in check helps in maintaining the project schedule. Overruns in labor often lead to delays, affecting the overall project timeline.
Tips for controlling construction labor costs
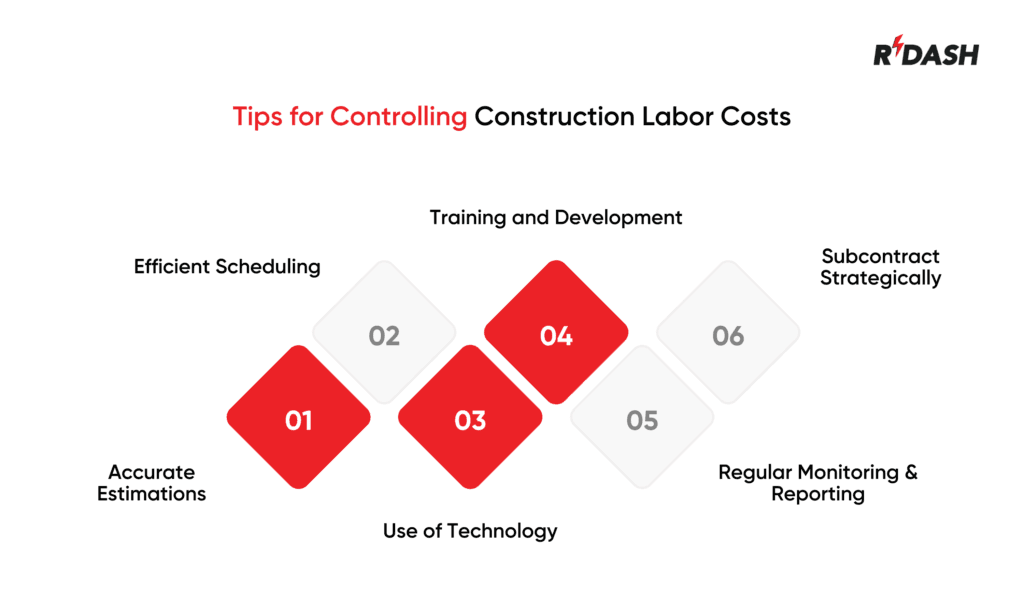
- Accurate Estimations: Begin with precise estimations of the labor required for each phase of the project. Use historical data and consider current market rates.
- Efficient Scheduling: Optimize the workforce schedule to minimize downtime and overtime. Implementing staggered shifts or flexible working hours can also reduce bottlenecks and improve productivity.
- Use of Technology: Implement project management and workforce scheduling software like RDash to streamline operations and improve communication.
- Training and Development: Regular training helps improve worker efficiency, reducing the time it takes to complete tasks which, in turn, lowers labor costs.
- Regular Monitoring and Reporting: Keep track of labor productivity and costs through continuous monitoring. This enables timely adjustments before costs overrun.
- Subcontract Strategically: Use subcontractors for specialized tasks where they can perform work more efficiently than general laborers, potentially reducing overall costs.
FAQs on construction labor cost
What factors influence construction labor costs?
Labor costs are influenced by project scope, local labor rates, duration of the project, and the physical demands of the job which may require specialized skills.
How can overtime impact labor costs in construction?
Overtime can significantly increase labor costs, especially when not managed correctly. Planning ahead can mitigate unexpected overtime, keeping costs within budget.
What is the role of automation in reducing labor costs?
Automation can streamline many construction processes, reducing the need for labor for repetitive tasks and thereby cutting costs.