What is construction supply chain management?
Construction Supply Chain Management (CSCM) refers to the comprehensive process of managing the flow of resources — from raw materials and equipment to services and information — required for the construction sector. It involves coordinating and optimizing all steps from initial material sourcing to final delivery, ensuring that construction projects receive the right materials, at the right time, and at the best cost.
Key components of a construction supply chain:
1. Key People-Related Components:
- Project Managers: Oversee the project from start to finish, ensuring all supply chain activities align with project timelines and budgets.
- Suppliers and Contractors: Provide the necessary materials, labor, and services, requiring careful selection and management to maintain quality and efficiency.
- Logistics Coordinators: Manage the transportation and storage of materials, critical for timely delivery and minimizing holding costs.
2. Key Activity-Related Components:
- Procurement: Involves selecting and acquiring the various resources needed for the project while negotiating favorable terms.
- Material Management: Ensures that the right materials are available in the correct quantities at the right time, without excessive inventory.
- Information Management: Uses technology to provide accurate and timely information across the supply chain, enhancing decision-making and responsiveness.
Understanding and managing these components effectively can lead to reduced costs, increased efficiency, and successful project execution in the construction industry.
What makes supply chain management hard in construction?
Supply chain management in construction is particularly challenging due to the complexity and scale of most projects. Factors that contribute to these difficulties include:
- Multiple Stakeholders: Construction projects typically involve a large number of parties, including architects, contractors, subcontractors, suppliers, and clients. Each has different priorities and schedules, complicating coordination.
- Customization and Variability: Each construction project is unique, often requiring custom materials and techniques which can introduce variability and unpredictability into the supply chain.
- Environmental and Regulatory Factors: Construction must comply with numerous local, regional, and national regulations which can change unexpectedly and impact supply chain logistics.
- On-Site Challenges: Issues such as limited storage space, the need for just-in-time delivery, and the impact of weather or other delays can disrupt the supply chain.
Who Is involved in the construction supply chain?
The construction supply chain involves various key players who ensure that all necessary resources are available as needed throughout a project. These include:
- Suppliers: Provide raw materials and specialized products necessary for construction.
- Manufacturers: Produce and supply construction materials, equipment, and systems.
- Contractors and Subcontractors: Execute the construction work, relying on timely deliveries and proper scheduling.
- Project Managers: Oversee the entire project, ensuring that every aspect of the supply chain aligns with the project’s timeline and standards.
- Logistics Providers: Manage the transportation and distribution of materials to ensure they arrive on time and in good condition.
Each participant plays a crucial role in maintaining the flow of materials and information, making effective communication and coordination essential for successful construction supply chain management.
How SCM works in construction
Supply Chain Management (SCM) in construction coordinates all aspects of the supply process, ensuring that every element needed for a construction project is available at the right time and place. Here’s how it generally works:
- Planning: Before any physical work begins, effective SCM requires detailed planning. This includes assessing project needs, forecasting demand for materials, and scheduling deliveries based on the project timeline.
- Sourcing: Identifying and selecting suppliers who can provide the necessary materials, equipment, and services at the required quality and price.
- Ordering: Placing orders with chosen suppliers ensuring that procurement aligns with project schedules and budget constraints.
- Logistics: Coordinating the transportation and storage of materials to ensure they arrive on time and in usable condition, which might involve sophisticated logistics planning especially for projects in congested urban areas or remote locations.
- On-site Management: Managing on-site inventory, ensuring that materials are properly stored and available as needed to avoid delays or disruptions in the construction process.
- Monitoring and Controlling: Continuously monitoring the supply chain to address any issues promptly and making necessary adjustments to schedules, orders, or supplier choices.
The benefits of better supply chain management in Construction
Improved supply chain management in construction brings several significant benefits:
- Cost Efficiency: Reducing waste through precise order quantities and improved material handling cuts costs significantly.
- Timely Project Completion: Ensures that projects stay on schedule by avoiding delays caused by material shortages.
- Quality Assurance: Maintains high-quality standards by ensuring that the right materials that meet specified standards are used.
- Flexibility and Adaptability: Enhances the ability to respond to unexpected changes or challenges during the construction process.
- Risk Management: Minimizes the risk of project delays and cost overruns by proactively managing supply chain vulnerabilities and dependencies.
Strategies to improve construction supply chain management
Improving supply chain management in the construction industry involves strategic planning and proactive measures to enhance efficiency and reduce risks. Here are key strategies:
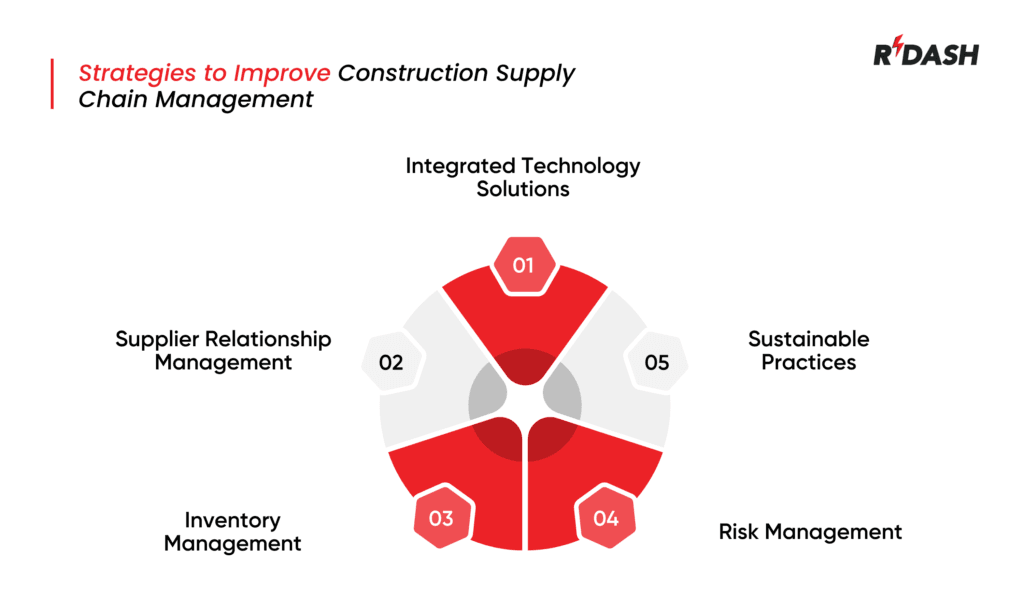
- Integrated Technology Solutions: Utilizing advanced software solutions like RDash can streamline processes from procurement to project management, improving communication and data accuracy across all stages of the supply chain.
- Supplier Relationship Management: Building strong relationships with suppliers ensures reliability and quality in the supply of materials and services. Regular communication and performance reviews can help maintain these relationships.
- Inventory Management: Efficient inventory management practices can minimize waste and ensure that materials are available when needed. This involves accurate demand forecasting and storage solutions that preserve material quality.
- Risk Management: Identifying potential risks in the supply chain and developing mitigation strategies is crucial. This includes having contingency plans for supply disruptions and diversified supplier networks to reduce dependency on a single source.
- Sustainable Practices: Implementing sustainable procurement practices not only contributes to environmental stewardship but also can enhance the company’s reputation and compliance with regulations.
Construction Supply Chain Trends in 2025
In the year 2025, several trends are likely to influence the construction supply chain:
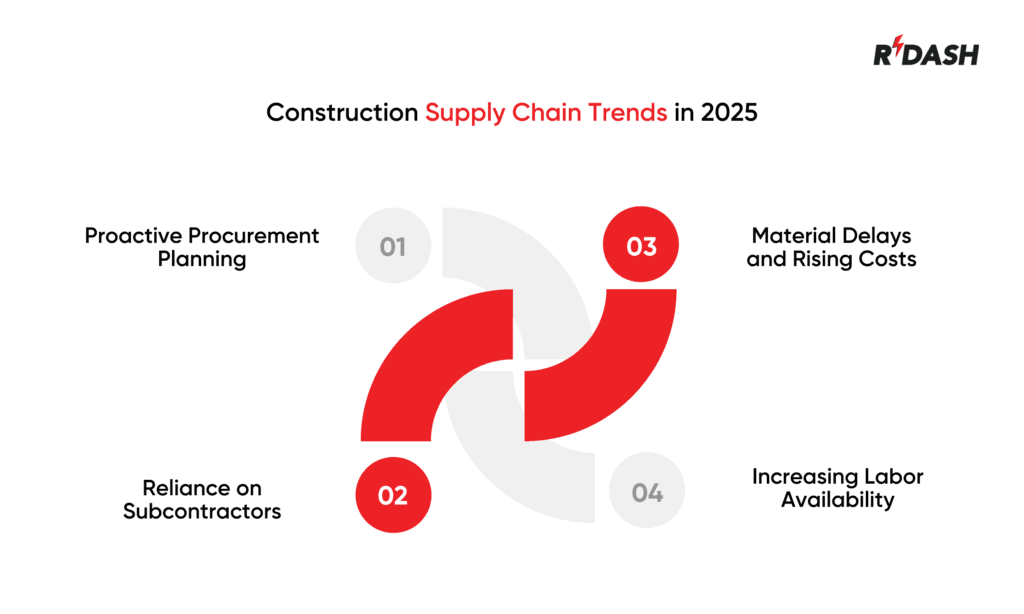
- Proactive Procurement Planning: Anticipating needs and making procurement decisions well in advance to avoid delays and capitalize on market conditions.
- Reliance on Subcontractors: Increasing use of subcontractors to manage specialized aspects of projects, requiring tight integration and coordination.
- Material Delays and Rising Costs: Ongoing challenges with global supply chains may continue to cause delays and increase material costs, making effective supply chain management even more critical.
- Increasing Labor Availability: As the labor market adjusts, there may be more opportunities to secure skilled labor, potentially easing some of the workforce challenges faced by the industry.
How RDash Can Enhance Supply Chain Management in Construction
RDash significantly bolsters supply chain management by offering robust tools tailored for the dynamic needs of the construction industry:
- Document and Communication Management: RDash streamlines the flow of information across all parties involved in the project. By centralizing document storage and communication, it ensures that everyone from suppliers to subcontractors has access to the latest updates, reducing misunderstandings and delays.
- Cost Management and Budget Tracking: Effective financial oversight is crucial in construction. RDash provides detailed cost tracking and budget management tools, allowing project managers to monitor expenditures in real time, compare them against the budget, and make informed decisions quickly.
- Real-time Inventory Tracking: Keeping a close eye on material availability and location can make or break project timelines.