What are construction SOPs?
Construction Standard Operating Procedures (SOPs) are detailed, written instructions designed to achieve uniformity in performing specific functions. SOPs in construction lay out the steps that workers and management should follow to carry out tasks efficiently and safely. This can include everything from how to prepare a site before work begins to how to handle materials or operate machinery. The purpose of SOPs is to ensure that work is done consistently and correctly across all projects, minimizing errors and maximizing safety.
Why do construction companies adopt SOPs?
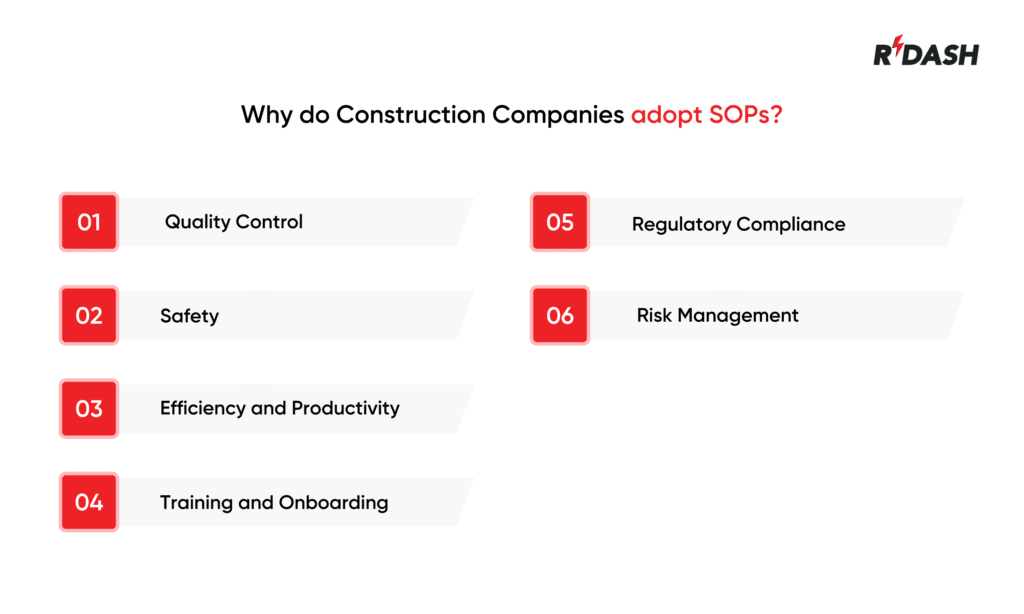
Construction companies adopt SOPs for several important reasons:
1. Consistency and Quality Control:
Construction SOPs help ensure that every task, no matter who completes it or where it is done, meets the same high standards. This consistency is crucial for maintaining quality across all construction projects, which can enhance the company’s reputation and client satisfaction.
2. Safety:
One of the biggest benefits of having SOPs is the enhancement of safety on construction sites. SOPs outline the proper procedures to follow, which can help prevent accidents and injuries. This is particularly important in an industry that can be dangerous, with risks from heavy machinery, heights, and more.
3. Efficiency and Productivity:
When workers have clear instructions on how to perform tasks, they can do their work more quickly and efficiently. SOPs eliminate the need for workers to guess how to do something or to stop work to ask questions. This streamlining of processes can lead to significant improvements in productivity.
4. Training and Onboarding:
For new employees, SOPs provide a valuable resource for understanding how various tasks should be performed. This is crucial for bringing new team members up to speed quickly and effectively, ensuring they contribute to the project without extensive delays.
5. Regulatory Compliance:
In construction, adhering to regulatory standards is not just important – it’s often legally required. SOPs help ensure that companies comply with all relevant laws and regulations, which can include building codes, environmental protections, and labor laws.
6. Problem Solving and Risk Management:
When issues do arise, having SOPs in place can help managers and workers quickly find solutions. By following procedures that have been proven effective, teams can resolve problems more rapidly and prevent small issues from becoming larger crises.
What makes a good SOP?
For a construction SOP to be effective, especially in the high-stakes environment of construction, it needs to be:
1. Understood:
A good SOP should be clear and straightforward, using simple language that can be easily understood by everyone who needs to follow it. Avoid technical jargon unless it is commonly understood by the workforce, or provide definitions for any technical terms used.
2. Documented:
An SOP must be written down and accessible. This documentation acts as a permanent reference that can be consulted to ensure tasks are completed correctly. It should be stored in a way that is easy for all relevant team members to find and use, such as on a company intranet or in a shared digital document.
3. Agreed Upon:
Before an SOP can be implemented, it must be agreed upon by all parties involved in the process it describes. This includes the workers who will follow the SOP, as well as supervisors and any other stakeholders. Agreement ensures that everyone is on the same page and commits to following the SOP.
Construction SOPs categories
SOPs in the construction industry can generally be divided into two main categories:
1. How-to’s:
These SOPs provide step-by-step instructions on how to perform specific tasks. This could include how to operate a piece of machinery, how to conduct a safety inspection, or how to execute a particular construction technique. How-to SOPs are essential for training new employees and ensuring consistent performance across the board.
2. Essential Processes:
These SOPs outline the processes that are critical to the successful completion of a construction project. This might include procedures for quality control checks, compliance with regulatory requirements, or the steps to follow when escalating an issue. Essential process SOPs help ensure that critical project elements are handled efficiently and effectively, maintaining project integrity and safety.
Where to start with construction SOPs

Starting with Construction SOPs in the construction industry involve a strategic approach to ensure that the processes contribute effectively to the organization’s operations. Here are some steps to get started:
1. Identify Key Processes: Begin by identifying the core processes that need standardization within your organization. Focus on areas where consistency and safety are critical, or where there is significant risk of non-compliance with regulations.
2. Gather Input: Consult with teams across different levels – especially those who are directly involved in the processes. Their insights are valuable in understanding the practical aspects of the tasks and the common issues they face.
3. Prioritize: Not all processes need SOPs at the same level of urgency. Prioritize creating SOPs based on the criticality of the process to business operations, the complexity of tasks, and the risk involved.
4. Draft the SOP: Write the SOP using clear, concise language. Include detailed steps, expected outcomes, and safety notes. Visual aids like diagrams or photos can enhance understanding.
5. Review and Revise: Have the SOP reviewed by team leaders and legal or compliance experts to ensure it covers all necessary aspects and complies with applicable regulations.
6. Train and Implement: Once the SOP is finalized, organize training sessions for all relevant staff. Ensure everyone understands the SOP before it is fully implemented.
7. Monitor and Update: Regularly review and update the SOP to ensure it remains relevant and effective. Changes in regulations, technology, or company processes may necessitate updates.
Do’s and Don’ts of creating and implementing construction SOPs
Do’s:
- Do involve the actual users in the writing process to ensure the SOP is practical and clear.
- Do keep the language simple and straightforward to avoid misunderstandings.
- Do use visuals where possible to clarify complex steps.
- Do regularly review and update the SOPs to keep them current with technological and regulatory changes.
- Do ensure accessibility of the SOPs to all employees who need them.
Don’ts:
- Don’t overload SOPs with too much information that can overwhelm the users. Keep them focused and to the point.
- Don’t use technical jargon unless absolutely necessary, and always provide clear definitions.
- Don’t skip the training on SOPs. Ensure everyone understands the SOPs before they are expected to follow them.
- Don’t ignore feedback from employees. Continuous improvement is key to effective SOPs.
- Don’t overlook compliance aspects while drafting SOPs. Always consider legal and safety requirements.
Challenges in implementing construction SOPs
Implementing Construction SOPs can bring about significant improvements in efficiency and safety. However, the process comes with its own set of challenges that organizations need to navigate carefully. Here are some common hurdles:
1. Resistance to Change:
One of the biggest challenges is resistance from employees who are accustomed to existing processes. Changing long-standing practices can be met with skepticism and reluctance, particularly from those who may not immediately see the benefits of the new SOPs.
2. Inadequate Training:
For SOPs to be effective, thorough training is necessary. However, inadequate training can lead to misunderstandings and incorrect implementation of the procedures, which defeats the purpose of establishing SOPs in the first place.
3. Complexity of Documentation:
Creating clear and concise SOPs that are easy to follow can be difficult, especially for complex tasks. Overly complicated or poorly written SOPs can confuse workers, leading to errors and non-compliance.
4. Keeping SOPs Updated:
The construction industry is dynamic, with frequent changes in technology, materials, and regulations. Keeping SOPs updated with these changes can be a continuous challenge that requires regular review and revision processes.
5. Ensuring Compliance:
Ensuring that all SOPs comply with the latest safety and industry regulations is crucial but challenging. Non-compliance can lead to legal issues and safety hazards on the job site.
Construction SOPs FAQs
Why are SOPs important in construction?
Construction SOPs ensure that work is performed consistently and safely across all projects, reducing the risk of accidents and ensuring quality control. They also help in meeting regulatory requirements and improving overall project efficiency.
How often should construction SOPs be updated?
Construction SOPs should be reviewed and updated regularly, at least annually, or whenever there are significant changes in technology, materials, work processes, or compliance requirements.
Who should be involved in creating construction SOPs?
Developing effective SOPs should involve input from various stakeholders including project managers, site supervisors, safety officers, and the workers who perform the tasks. Involving a legal or compliance expert is also beneficial to ensure all regulatory aspects are covered.
How can resistance to construction SOPs be overcome?
Resistance can be overcome by involving employees in the development process, clearly communicating the benefits, providing comprehensive training, and gradually implementing changes to allow adjustment time.
Can technology help in managing SOPs?
Yes, technology such as project management software and mobile apps can help in creating, distributing, and updating SOPs more efficiently. They also provide easy access to Construction SOPs on the job site, ensuring that all team members follow the latest procedures.
Next Read: What Does a Construction Supervisor Do?